对螺杆空压机机头温度超高现象的原因进行分析、论证,并就各个原因提出了相应的解决方案,为空压机的良好运行提供强有力的保障。
螺杆压缩机工作流程:空气自空气过滤器和卸荷阀组件吸入,进入压缩机主机进行压缩,压缩后的油气混合物进入油分离器,完成油气分离。之后,压缩空气经最小压力阀进入空气冷却器,冷却后的压缩空气经气水分离器和供气阀向气网供气。而从油分离器分离出的油进入油冷却器,冷却后的油经油过滤器和断油阀向压缩机机头供油,完成油路循环。
螺杆空压机机头是靠润滑油润滑、降温的,因此润滑油系统直接影响机头温度。而润滑油是靠风冷(冷却水)降温的,因此风冷(冷却水)系统又直接影响润滑油的温度。再有控制系统故障,排气压力超过设定值,压缩机不减载,导致空压机运行功率增大,机头温度升高。从以上三个方面对机头温度高的原因进行分析,见下表:
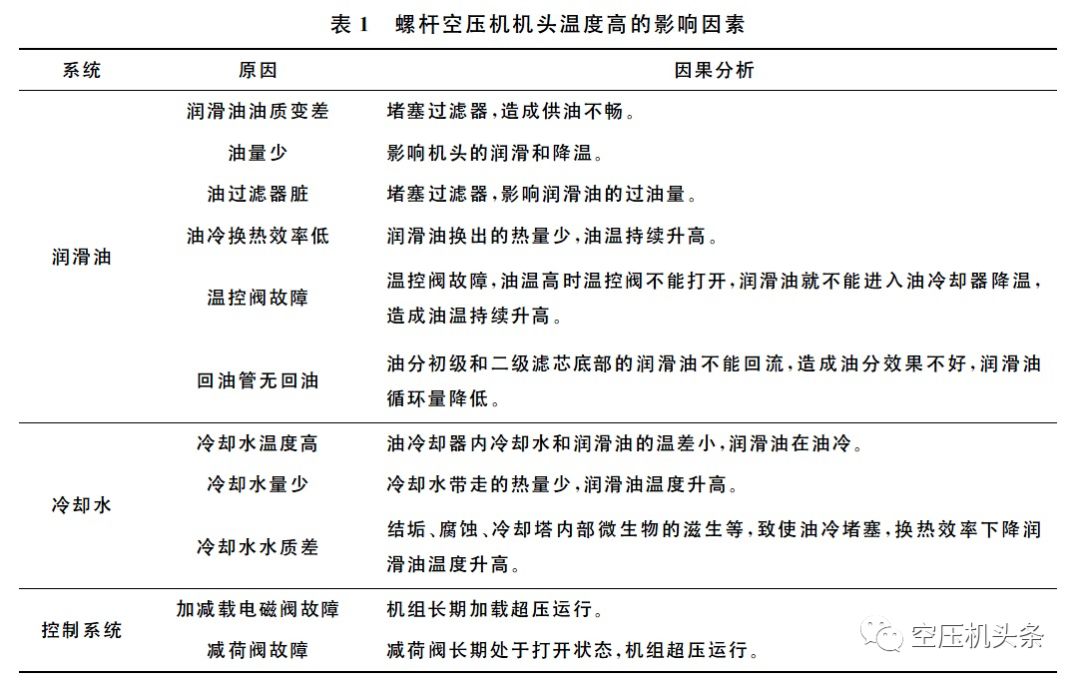
3.1.1润滑油油质变差
为避免油质变差,车间结合设备部对润滑油油质每半年化验一次,一旦出现碳化和结胶等不合格的情况,必须更换润滑油。换油前必须更换油滤和油分滤芯,并用新润滑油清洗油路系统。然后添加润滑油至合适油位。
压缩机油气分离器上都装有1个视油镜。压缩机满载运行时从视油镜能观察到油位在试镜的上下刻度线之间即可,如果低于下刻度线,需添加注润滑油至满载运行时能够观察到油位在视油镜的1/2~3/4为佳。
操作人员应根据控制器面板上显示的信号,及时更换滤芯。拆下油过滤器,检查油过滤器堵塞情况,轻者用压缩空气吹来清除杂质,堵塞严重的就更换油过滤器滤芯,增大机头供油量。油过滤器顶部设有压差传感器。当滤芯前后的压差超过设定的压力时,监控器的面板上就会显示维护信号,提醒机组操作人员及时更换滤芯。油过滤器的滤芯应定期更换,以保证油路畅通。
油冷却器为壳管式冷凝器,水走管程,油走壳程。水路结垢时,用除垢剂配成水溶液,在冷却水管路打循环3~4h,然后用清洗机清洗换热铜管内部。如果油路出现油污堵塞翅片等现象,应用煤油或除油剂进行清洗。这样,将油冷的管程和壳程清理后,会大大提高油冷却器的换热效果。
温控阀内部阀芯可以拿下来放在开水里面,看看阀头会不会伸缩。阀头遇到高温时会伸出来,冷得时候缩进去。如果感觉拆下来麻烦的话,可以启动压缩机,让压缩机油温上升。温控阀上面总共有三根油管,一根连接油气桶,一根连接油滤,一根连接冷却器。当机组刚启动时,油温还低的时候,油气桶内部润滑油到了温控阀后,直接进油滤过滤后回主机头里面,不经过冷却器冷却,如果温控阀正常,连接油滤的那根油管应该是凉的,连接冷却器的油管是热的。当油温高了后,温控阀内部阀芯遇高温润滑油,自动伸缩控制,你可以用手去摸一下温控阀的两根出油管,即一根连接油滤,一根连接冷却器的,如果温控阀正常的,连接油滤的那根油管应该是凉的,连接冷却器的油管是热的。
回油管上设有视油镜、供操作人员观察回油情况。压缩机满载时,应有较大流量。卸载时,流量很小,甚至没有。若回油管过滤器堵塞或回油管未插入油分初级和二级滤芯底部,润滑油不能回流。若满载时断流或流量很少,应停机卸压后清洗回油过滤器或重新将回油管插入油分底部。
冷却水的温度应≤30℃。冷却水温高,首先我们可以检查冷却塔的运行,根据情况调节冷却塔百叶的开度、根据风机电流调节风机扇叶开度,增开风机。而当夏季环境温度高、湿度大的情况下,冷却塔风机降温效果差,我们可以辅助向水池填加低温深井水(温度一般在20℃左右),并将高温循环水部分排入生产水池,可将冷却水整体温度降低3~4℃。前提要保证循环水池水位平衡。
检查冷却水压力和冷却水进出水温差。如果冷却水压力低,且冷却水进出水温差大,说明冷却水量不足。一般进水压力应大于等于0.25MPa,冷却水进出水温差控制在5~10℃。根据压力和温差情况调整冷却水泵的运行。
为使冷却器保持良好的换热效果,延长冷却器的使用寿命,必须使用洁净的冷却水。冷却水应接近中性,即pH值应在6.5~9.5之间;有机物质和悬浮机械杂质应小于L25mg/L;含油量小于5mg/L;暂时硬度≤10℃(硬度1°相当于是1升水中含有10mg/L CaO或7.19mg/L CaO)。冷却水应优先选用软水。而且需在循环冷却水中添加缓蚀阻垢剂,防止水垢的形成。为防止微生物的滋生,还需加入杀菌灭藻剂,来改善冷却循环水水质。
检测加减载电磁阀的通断情况是否正常。如果不动作,说明电磁阀故障,应检查或更换电磁阀。
检查调压阀是否堵塞、漏气和脱落。如果出现以上状况,立即清理并安装。如不可修复,立即更换。
以上是综合几年来的运行经验总结出的有效解决方法。在以后遇到这种问题时能在短时间内正确分析和判断,找出故障点,及时快速处理。减少了对设备的损害,防止事故的蔓延,延长设备的使用寿命。
本站系本网编辑转载,转载目的在于传递更多信息,并不代表本网赞同其观点和对其真实性负责。如涉及作品内容、版权和其它问题,请在30日内与本网联系,我们将在第一时间删除内容![声明]本站文章版权归原作者所有 内容为作者个人观点 本站只提供参考并不构成任何投资及应用建议。