氢气压缩机气阀断裂分析及试车方案改进氢气压缩机气阀断裂分析及试车方案改进 李洪深1,刘 鹏2,李十中1 (1.清华大学核能与新能源技术研究院,北京100084;2.中国天辰工程有限公司,天津300400)......
(1.清华大学核能与新能源技术研究院,北京100084;2.中国天辰工程有限公司,天津300400)
[摘 要]:针对某往复氢气压缩机排气阀在空气试车过程中出现的气阀断裂失效的实际问题,初步分析了气阀断裂部位、结构和工作特性。研究了发生断裂的气阀阀座危险截面在正常载荷和冲击载荷作用下的受力情况,重点分析了影响阀片冲击载荷变化的主要因素。研究结果表明,试车过程中气阀失效主要受阀片密度和冲击速度变化影响。结合现场试车时的实际操作工况,确定了气阀断裂的主要原因。从工程设计角度,提出了往复式氢气压缩机试车方案的改进措施,研究结果可以为今后同类压缩机空气试车方案的制定提供参考。
[关键词]:往复压缩机;网状阀;负荷试车;失效分析
文章编号:1006-2971(2022)03-0016-0
氢气是极具发展潜力的清洁能源和重要的化工原料。随着我国加紧布局氢能产业,高压加氢站的建设逐渐成为制约氢能产业发展的瓶颈[1]。作为原
料,氢气在合成氨、煤化工、重整制氢等生产流程中,也需要在较高的压力下进行化学反应[2]。在所有压缩机类型中,往复压缩机能提供最高的压缩比,是氢气储运的关键设备,其运行状况的好坏往往决定整个工程项目的成败。
气阀是往复压缩机的核心部件,安装在气缸上,控制着压缩机的吸气、排气过程。由气阀原因导致的压缩机故障约占故障总数的36%,且更换气阀成本较高,因此气阀的可靠性成为压缩机运行经济、安全、可靠的关键[3]。
目前,对往复压缩机运行中的故障模拟、诊断和报警系统国内外已有较多研究[4,5],但压缩机在单机试运转过程中缺少系统保护,且所用试验气体与工作气体存在较大差距,易发生故障,却缺少相应的解决方案。针对这一问题,本研究尝试对某氢气化工项目试车过程中发生故障的氢气压缩机气阀进行失效分析,并提出相应的试车方案的改进措施。
某化工项目中使用的氢气压缩机为4列4级往复压缩机,进口压力0.11MPa(A),压缩比16。在使用空气进行单机负荷运转试验过程中,该压缩机3级气缸的4个排气阀从中间整体断裂。
空气试车前,根据现场条件制定的压缩机负荷试运转程序如下:
(1)压缩机吹洗运转合格后,接好各部管路并关闭排气口与系统连接的截止阀。
(4)启动循环系统稀油装置的辅助油泵,调整压力到规定要求。
(5)打开旁通阀,使压缩机各级成无载状况,并盘车两转,观察压缩机无异响时,即可脱开盘车装置,启动压缩机。
(6)关闭辅机排液阀,各级旁通阀,逐渐调节压缩机排气阀门,使压缩机缓慢升压至末级出口压力达到0.5MPaG,负荷运转时间不少于4小时。
负荷运转中检查项目有:四级排气温度小于150℃,机身主轴承温度小于65℃,活塞杆摩擦表面温度不超过100℃,检查漏气点作必要标记,检查各仪表、阀门、电机等工作是否正常等。
发生故障前,压缩机先后已经历3次不同负荷的运转试验,加载过程中发现三级排气阀有漏气现象,三级气缸有异响,机身振动大,因此未继续增加四级气缸的负荷,即未加压到规定的排气压力。试验后,拆卸检查气阀的过程中,发现三级排气阀阀座及升程限制器出现断裂。
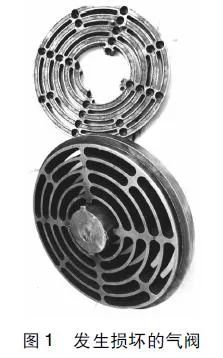
在压缩机负荷试验后,对损坏的三级排气阀的损坏情况做出记录。断裂位置如图1所示,气阀阀座中间螺栓与阀座之间在加强筋处拉断,升程限制器中心处发生断裂。位于阀座与升程限制器之间的阀片随升程限制器一同断裂,阀片碎片和弹簧散落。
根据以往项目设计经验,气阀阀片、弹簧、垫片等部件为易损件,为避免试车时损坏,采购有随机备件。而发生损坏的阀座和升程限制器等元件通常表现为中长期故障,只作为2年备件采购。因在现场找不到可代用的气阀组件,而重新采购供货周期长达3个月,使全厂试车无法顺利进行,最终导致该项目的交付工期受到严重影响。
在往复压缩机中,应用最广泛的气阀型式为网状阀。网状阀由阀座、阀片、弹簧、中间螺栓和升程限制器等部分组成,它依靠阀片的开启与关闭使气缸与外界接通与切断,阀片的开启与关闭由气缸内、外气体压力差与弹簧力控制,无需其他驱动机构。
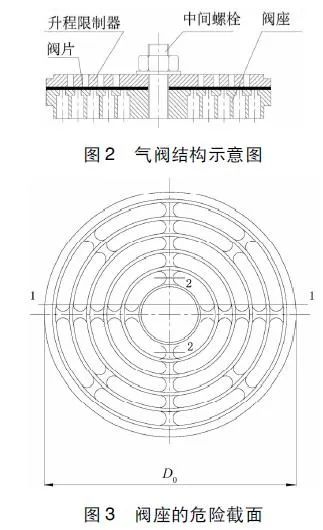
压缩机气阀结构如图2所示,网状阀阀座具有能被阀片覆盖的气体通道,与阀片一起控制压缩机的进气或排气,并承受气缸内外压力差。升程限制器限制阀片的升程,有着与阀座相似的气流通道,作为气阀弹簧的支承座,其上开有弹簧孔。阀座各环形通道间由径向加强筋连接。为防止相对转动,阀座和升程限制器之间采用中间螺栓联接,中间螺栓把升程限制器与阀座压紧在压缩机气缸的阀孔上。
故障压缩机排气阀的阀座、阀片和升程限制器都采用环形通道,升程限制器通道与阀座通道错开。当气缸与阀腔之间的气体压力差,足以克服弹簧力及阀片的质量力时,阀片开启。气体先流入阀座,经过环形通道进入气缸。气阀刚开启时,气流推力大于弹簧力,阀片被推向升程限制器;当活塞接近止点时,速度降低,进气速度和气流推力也相应减小,导致气流推力不足以克服弹簧力,阀片又推向阀座,并与阀座贴紧,如此循环往复。
根据故障压缩机气阀实际发生断裂的部位,对图3中2-2截面进行强度校核。这时阀座可以简化为由多段两端固定的梁承受全部气体力[9],如图
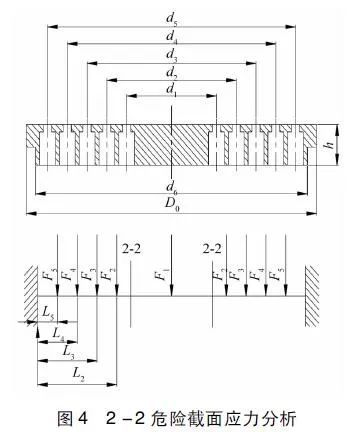
首先校核正常负载情况下的弯曲应力。阀座具体尺寸已经在图中标注,压缩机三级气缸在工作状态下的内外压差△p=0.32MPa,作用于最内圈通道的平均直径d1圆周上的气体力
阀座是在动载荷条件下工作的,承受和压缩机曲轴同频率变化的气缸内外压差和气阀开启关闭过程中的阀片撞击力。故障压缩机气阀阀座材料为3Cr13,其许用应力为[σ]=180MPa,仅在气体压力作用下,阀座加强筋的强度足够,而发生故障的部位又与校核截面位置吻合。这说明在没有超压试车的情况下,阀座的损坏很可能是由阀片过大的撞击力造成的。
升程限制器的气流通道与阀座气流通道的结构相同,径向加强筋布置也与阀座相同。因此其受力情况与阀座类似,承受气阀全开时气流的反作用力,其不同点在于,阀座靠气缸缸体支撑,而升程限制器靠固定于中间螺栓上的螺母支撑。排气阀升程限制器的加强筋内设置了弹簧孔和弹簧,阀片对升程限制器的冲击受到弹簧力的约束。因此,可以判断造成压缩机排气阀损坏的阀片冲击载荷必然先撞击阀座,导致危险截面处拉断,再通过弹簧力传导至升程限制器,由于中间螺母的挤压,导致升程限制器中心处断裂,随弹簧和阀片从排气阀脱落。
阀片在气流的作用下冲击阀座的过程伴随着复杂的发热、塑性变形和能量耗散,较为复杂,本研究在对阀片结构进行合理简化的基础上,选择使用能量法计算冲击应力[6]。
可以判断阀片的冲击载荷与阀片的运动速度、密度和弹性模量正相关。此外,阀片对阀座的撞击并非完全垂直,因气流不稳定和阀片质量不均匀,阀片会发生一定倾侧,当阀片侧倾运动幅度超过设计值后,撞击应力随侧倾运动幅度增大而迅速增加[7]。
故障压缩机阀片为非金属PEEK材料,密度和弹性模量符合设计标准[8],但由于在试车过程中采用的介质为空气,其密度是工作介质氢气密度的14.5倍,在相同的排气速度下,本身就增加了阀片对阀座的冲击力。更重要的是,由于试车时拆除了进口过滤器,前几次试车时的累积进气,导致空气中的灰尘、水分和气缸中高粘度润滑油不断在阀片上的沉积,阀片的密度不断增加;这些杂质堆积在阀片的不同部位,使原本质量分布均匀对称的阀片产生较大的质量不平衡力,这将极大的增加阀片的侧倾运动幅度,从而使冲击应力进一步扩大。
其次,试车前未对气量调节阀仪表气压力和气缸端盖螺栓预紧力进行检查,致使排气阀升程过大,而加速阀片的运动。再次,故障压缩机出口气量有多种工况组合,试车时频繁变化的排气负荷增加了扰动载荷,空气扰动同样增加了阀片的侧倾效应。在各因素的叠加作用下,最终导致冲击载荷超出阀座危险截面处的断裂强度,阀座从中间螺栓处拉断,进而损坏升程限制器,引起压缩机气阀的整体失效。
4 结论
根据以上分析结果,可以看出排气阀在试车过程中的损坏,主要是由以下原因造成的:
(1)压缩机设计时,未预留试车空气进气口,试车时只能将进口过滤器拆掉,空气中的灰尘、水分在阀片上堆积,增加了阀片密度。
(2)杂质在阀片上的不均匀堆积,增加了阀片的侧倾角度,进而增大阀片的冲击应力。
(3)气阀升程在试车前未校核,造成动载荷对阀座冲击速度过大。
(4)试车过程中频繁变化排气负荷,启动时电机转速不稳,气阀垫片损坏导致气体泄漏等原因增加了扰动载荷,进一步扩大了阀片的侧倾效应。
(5)气缸中高粘度润滑油施加过量,润滑油间接随空气附着在阀片,使更多空气中带入的灰尘,在阀片上的粘结。
因此,对往复式氢气压缩机的单机负荷试车程序提出以下改进措施,供今后类似工程项目参考:
(1)压缩机进口管道过滤器前增加空气试车接口,防止试车空气中的灰尘、水分进入气缸。在有条件的情况下,使用氮气代替空气进行运转试验更
(2)试车前必须仔细检查端盖螺栓预紧力,检查调节阀仪表压力,校核升程。
(3)调节流量时避免频繁的变化排气负荷,至少在同一负荷下运转30min。
(4)润滑油站不得超压,对可能的漏油点应及时检查。
(5)当试车时发生漏气现象时,必须及时停机检查,由于垫片原因导致泄漏时,及时更换垫片。
[1] 赵永志,蒙波,陈霖新,等.氢能源的利用现状分析[J].化工进展,2015,(34):3248-3255.
[2] 凌文,刘玮,李育磊,等.中国氢能基础设施产业发展战略研究
[J].中国工程科学,2019,(21):76-83.
[3] G.Sdanghi,G.Maranzana,A.Celzard,V.Fierro,Review oftheCurrentTechnologiesandPerformancesofHydrogenCompressionforStationaryandAutomotiveApplications,Renew.Sust.Energ.Rev.,2019,(102):150-170.
[4] 毕文阳,江志农,刘锦南.往复压缩机气阀故障模拟实验与诊断研究[J].流体机械,2013,(41):6-10.
[5] 刘卫华,郁永章.往复压缩机故障诊断方法的研究[J].压缩机技术,2001:3-5+12.
[6] P.Bialek,P.Bielawski,Failure Analysis of Hydrogen PistonCompressors,in:6thInternationalCongressonTechnicalDiagnostics
(ICTD),Gliwice,POLAND,2016,pp.69-80.
[7] B.L,N.H.,P.R..TheExcessEnergyApproachtotheImpactTestingofPlastics,Elsevier,1985,(5).[8] 卢朝霞,王玉鹏,张增营,等.往复式压缩机环状阀工作过程冲击应力分析[J].流体机械,2008:11-16.
[9] API,石油、化工和天然气工业设备用往复式压缩机[S].美国国家标准学会,2008.
本站系本网编辑转载,转载目的在于传递更多信息,并不代表本网赞同其观点和对其真实性负责。如涉及作品内容、版权和其它问题,请在30日内与本网联系,我们将在第一时间删除内容![声明]本站文章版权归原作者所有 内容为作者个人观点 本站只提供参考并不构成任何投资及应用建议。